Industrial Rail Trolley Multi-Station Auto Dispatch
The scheduling and implementation of the multi-station automatic material transportation of rail transfer cart involve multiple technologies and strategies. The following are some key steps and methods:
25 Ton Transfer Cart On Railway Video
System Architecture and Hardware Configuration
Track and transfer cart: Design and lay a track network suitable for material transportation. The track can be designed in various forms such as straight lines, curves, and rings to adapt to different production environments and spatial layouts.
Select a suitable transfer cart type, such as RGV (rail guided vehicle), to ensure that transfer trolley can run stably and quickly on the track.
Communication and control system: Establish a reliable communication network, such as Ethernet, wireless LAN, etc., to achieve real-time communication between rail transfer trolley and the main control system.
Select a high-performance control system, such as PLC (programmable logic controller), which is responsible for receiving task information, processing data, and issuing control instructions.
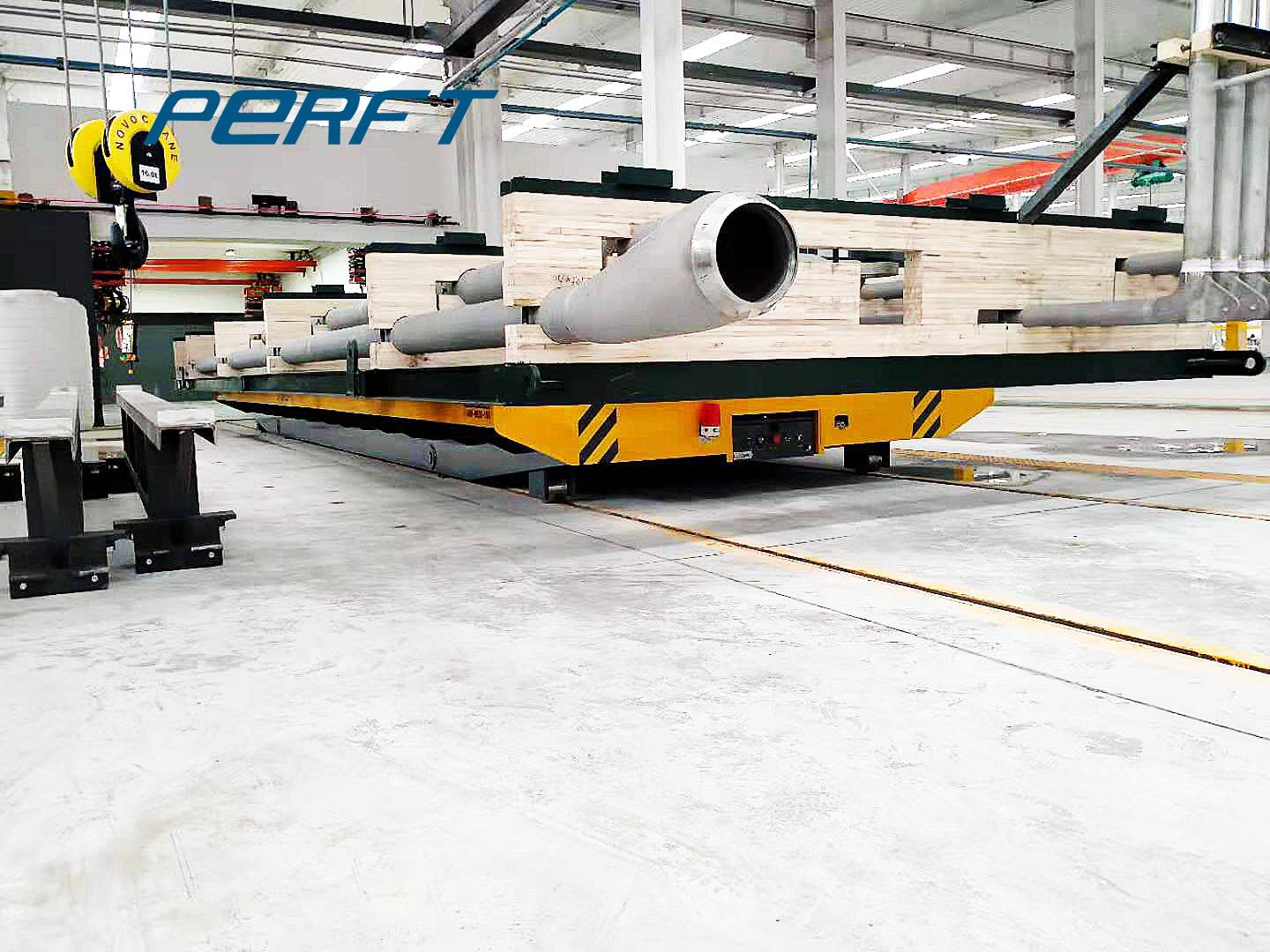
Scheduling Strategies and Algorithms
Task allocation: The main control system allocates tasks to appropriate transfer carts on rail according to production plans and material requirements. The scheduling algorithm should consider factors such as the current position of motorized transfer cart, task priority, material type, and station requirements to ensure the rationality and effectiveness of task allocation.
Path planning: Plan the optimal path for electric transfer cart based on task requirements and track layout. The path planning algorithm should consider factors such as track length, number of curves, and transfer cart speed to reduce transportation time and energy consumption.
Conflict resolution: In multiple transfer cart systems, path conflicts and resource contention may occur.
Adopt advanced scheduling algorithms and conflict resolution strategies, such as time window algorithms and path replanning, to ensure coordinated operation between motorized transfer carts.
Execution and Monitoring
Rail transfer cart execution: After receiving the control command, motorized transfer cart automatically runs according to the planned path and speed.
During the operation, transfer trolley should be able to detect its own status and environmental changes in real-time, such as track conditions, material location, etc., to ensure the accuracy and safety of transportation.
Monitoring and feedback: Establish a complete monitoring system to track the operation status and task execution of rail transfer trolley in real-time.
When an abnormal situation occurs, the system should be able to automatically alarm and take corresponding emergency measures.
Through data analysis and feedback, the scheduling strategy and execution efficiency are continuously optimized.
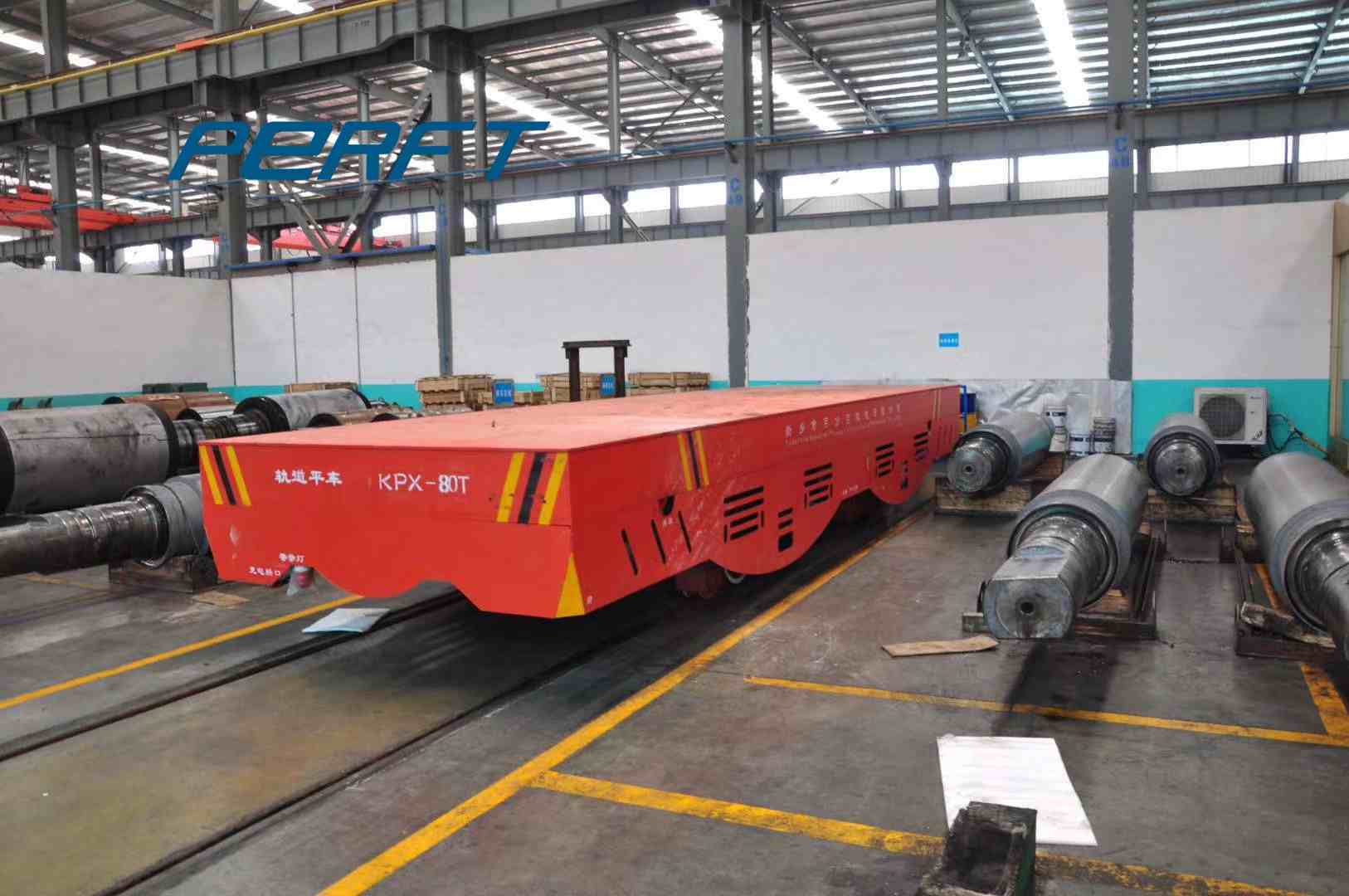
Optimization and Improvement
System optimization: Regularly maintain and upgrade the system to improve the stability and reliability of the system. According to changes in production needs, optimize and improve the track layout, transfer trolley type, scheduling algorithm, etc.
Efficiency improvement: By adopting advanced control technology, optimizing scheduling strategies, and increasing transfer trolley speed, the transportation efficiency and production efficiency of the system are continuously improved.
The scheduling of industrial rail trolleys for multi-station automated material transportation is a complex and systematic project. Through reasonable system architecture and hardware configuration, effective scheduling strategies and algorithms, strict execution and monitoring, and continuous optimization and improvement, the system can be ensured to operate effectively and stably, providing strong support for the production and development of enterprises.
Back to List